Innovation in Stacker Level Detection: Ultrasonic Sensors Replacing Contact-Based Material Hammers
Application of Ultrasonic Sensors in Stockpile Level Detection at a Stone Processing Plant
Original Solution: Working Principle of the Contact-Based Detection System
New Solution: Working Principle and Selection of Ultrasonic Sensors
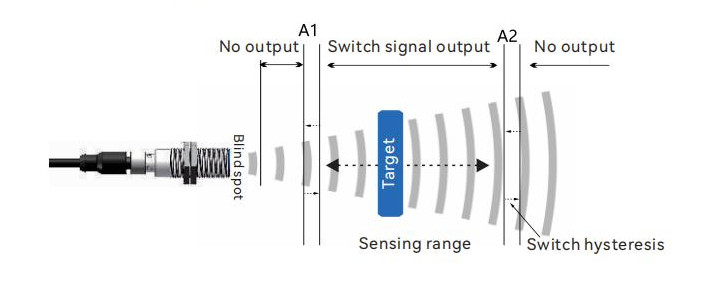
CSB30 Series Ultrasonic Sensors
Models
|
CSB30-2000 |
CSB30-4000
|
CSB30-6000
|
Detection range | 100 mm - 2000 mm | 200 mm - 4000 mm | 350 mm - 6000 mm |
Blind zone
|
0 mm - 100 mm |
0 mm - 200 mm
|
0 mm - 350 mm
|
Resolution
|
0.17 mm |
0.17-1.5 mm
|
0.17-2.5 mm
|
Response time | 82 ms | 162 ms | 232 ms |
Switching hysteresis | ±2 mm | ±4 mm | ±5 mm |
Switching frequency | 10 Hz | 5 Hz | 4 Hz |
Repeatability: ±0.15% of full-scale value | |||
Absolute accuracy: ±1 % (built-in temperature drift compensation) | |||
Input type: With synchronization and learning function | |||
Output type: Switch output; IO-Link output; Analog output; Digital output RS485 | |||
Material: Copper nickel plating , plastic fittings , glass filled epoxy resin | |||
Connection type: 5-pin M12 connector | |||
Protection Class: IP67 | |||
Ambient temperature: -25°C~+70°C (248~343K) |